Chemical plant safetyDebate over inherently safer technology (IST) at chemical plants intensifies
Recent accidents at chemical facilities around the country have prompt environmental groups and workplace safety advocates to highlight the need for implementing inherently safer technology (IST) at facilities using hazardous chemicals. IST is a methodology or an approach which calls for the adoption of a hierarchy of actions: minimize use of hazardous chemicals, substitute or replace hazardous chemicals with safer ones, moderate or shift to less hazardous chemicals or processes at lower temperatures and pressures, and simplify processes and design plants to eliminate unnecessary complexity.The industry argues that IST is a superficially simple concept but that, in reality, it is rather complex. For example, IST calls for facilities to reduce the amount of materials or chemicals they store on-site, which would increase transportation of the materials or chemicals, thus spreading the risk of chemical accidents to different points along the supply chain.
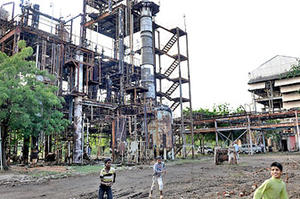
ISF seeks to avoid incidents rather than contain them // Source: chudu24.com
Recent accidents at chemical facilities around the country have prompt environmental groups and workplace safety advocates to highlight the need for implementing inherently safer technology (IST) at facilities using hazardous chemicals.
IST is a methodology that encourages substitution or minimization of hazardous materials, and the simplification of complex industrial processes which use hazardous materials. According to research scientist Anna-Mari Heikkilä, “an inherently safer design is one that avoids hazards instead of controlling them, particularly by reducing the amount of hazardous material and the number of hazardous operations in the plant.”
Chemical & Engineering News reports that IST proponents are asking regulators to mandate IST implementation, but some industry officials consider IST to be common sense, and say facilities could adopt IST standards as needed without a regulatory mandate.
“What we have now is risk management; what we need is risk prevention,” says Rick Hind, legislative director of the environmental group Greenpeace. “Risk management accepts the risk and simply cleans up the mess afterward. This isn’t acceptable and shouldn’t be acceptable to people who lost family members or their homes” in the recent accidents.”
An April 2013 ammonium nitrate explosion at a West, Texas fertilizer distributor claimed fifteen lives and injured 180 others. Since then, President Barack Obama has assigned a task force to explore ways to make chemical facilities safer and more secure. Led by the EPA, the Occupational Safety & Health Administration (OSHA), and DHS, the task force has until May 2014 to deliver recommendations. OSHA and state regulators do not currently require an IST assessment. C&EN notesthat the Chemical Safety & Hazard Investigation Board (CSB) is also exploring an IST mandate after a rash of refinery accidents, including one at a Chevron facility in Richmond, California which sent 15,000 residents to area hospitals.
IST was developed by Trevor Kletz, a chemical engineer with Imperial Chemical Industries, a British chemical company. For Keltz, IST functions well when implemented according to a hierarchy of actions: minimize use of hazardous chemicals, substitute or replace hazardous chemicals with safer ones, moderate or shift to less hazardous chemicals or processes at lower temperatures and pressures, and simplify processes and design plants to eliminate unnecessary complexity.