Rare Earth elements New magnets to reduce rare-earths dependence on China
China produces more than 95 percent of the world’s rare Earth elements, and Japan, the United States, and other industrial societies are increasingly anxious about the dependence of important sectors of their economies on Chinese whims; researchers are now working on new types of nanostructured magnets that would use smaller amounts of rare Earth metals than standard magnets; many hurdles remain, but GE Global Research hopes to demonstrate new magnet materials within the next two years
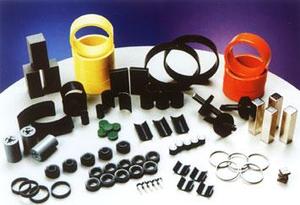
Assorted non-rare Earth magnets // Source: stanfordmaterials.com
Researchers are working on composites that would make strong magnets that need less of the hard-to-get rare Earth ingredients. Stronger, lighter magnets could enter the market in the next few years, making more efficient car engines and wind turbines possible. Researchers need the new materials because today’s best magnets use rare-Earth metals, the supply of which is becoming unreliable even as demand grows.
Technology Review reports that researchers are now working on new types of nanostructured magnets that would use smaller amounts of rare Earth metals than standard magnets. Many hurdles remain, but GE Global Research hopes to demonstrate new magnet materials within the next two years.
The strongest magnets rely on an alloy of the rare Earth metal neodymium that also includes iron and boron. Magnet makers sometimes add other rare Earth metals, including dysprosium and terbium, to these magnets to improve their properties. Supplies of all three of these rare earths are at risk because of increasing demand and the possibility that China, which produces most of them, will restrict exports.
It is not clear, however, whether the new magnets will get to market before the demand for rare Earth metals exceeds the supply. The U.S. Department of Energy projects that worldwide production of neodymium oxide, a key ingredient in magnets, will total 30,657 tons in 2015. In one of the DOE’s projected scenarios, demand for that metal will be a bit higher than that number in 2015. The DOE’s scenarios involve some guesswork, but the most conservative estimate has demand for neodymium exceeding supply by about 2020.
“A lot of the story about rare earths has focused around China and mining,” says Steven Duclos, manager of material sustainability at GE Global Research. “We believe technology can play a role in addressing this.” The DOE is funding GE’s magnet project, and one led by researchers at the University of Delaware, through the Advanced Research Projects Agency-Energy (ARPA-E) program, which fosters research into disruptive technology.
Coming up with new magnet materials is not easy, George Hadjipanayis, chair of the physics and astronomy department at the University of Delaware, told TR. Hadjipanayis was involved in the development of neodymium magnets in the 1980s while working at Kollmorgen. “At that time, maybe we all got lucky,” he says of the initial development of neodymium magnets. The way researchers made new magnets in the past was to crystallize alloys and look for new forms with better properties. This approach won’t work going forward. “Neodymium magnet performance has plateaued,” says Frank Johnson, who heads GE’s magnet research program. Hadjipanayis agrees. “The hope now is nanocomposites,” he says.
Nanocomposite magnet materials are made up of nanoparticles of the metals that are found in today’s magnetic alloys. These composites have, for example, neodymium-based nanoparticles mixed with iron-based nanoparticles. These nanostructured regions in the magnet interact in a way that leads to greater magnetic properties than those found in conventional magnetic alloys.
The advantage of nanocomposites for magnets is twofold: nanocomposites promise to be stronger than other magnets of similar weight, and they should use less rare-earth metals. What enables better magnetic properties in these nanocomposites is a property called exchange coupling. The physics are complex, but coupling between different nanoparticles in the composite leads to overall magnetic properties that are greater than the sum of the parts.
Exchange coupling can’t happen in pure magnet materials, but emerges in composites made of mixtures of nanoparticles of the same metals that are used to make conventional magnets. “The advantage of stronger magnets is that the machines you put them in can be smaller and lighter,” says Johnson.
GE would not disclose which materials it’s using to make the magnets, or what its manufacturing methods would be, but Johnson says the company will rely on techniques it has developed to work with other metals. The main problem the company faces, says Johnson, is scaling up production to make large magnets — so far it is only been possible to make thin films of the nanocomposites. The company has about $2.25 million in funding from ARPA-E.
Hadjipanayis reports his group, a multi-institute consortium, has received nearly $4.5 million in ARPA-E funding. It is possible to make the necessary nanoparticles in small quantities in the lab, but scaling up will be difficult. “They’re very reactive materials,” he says.
The group is experimenting with a wide range of different types of nanoparticles, including combinations of neodymium-based nanoparticles with iron-cobalt nanoparticles. Another challenge is assembling the nanoparticles in a mixture that ensures they have enough contact with each other to get exchange coupling. “It’s one step at a time,” says Hadjipanayis.