Futuristic constructionPrinting a building -- additive manufacturing research moves into construction
Additive manufacturing — commonly known as 3-D printing — has been used for a surprisingly large range of products and projects, while the devices themselves have continually declined in cost and size; now the technology turns its attention to concrete and building
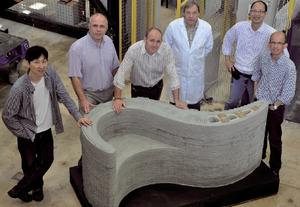
The Loughborough University team, with a printed concrete bench // Source: webbdevlam.com
Additive manufacturing, more commonly known as 3-D printing, has been in development and use for more than ten years. In that time, it has been used to create a surprising array of products, ranging from truly playable violins to jewelry and machine parts.
At the same time, the size and cost of 3-D printers has dropped dramatically. The industry has seen continued growth in sales, and even offers a desktop model to produce design prototypes. The technology has arrived at the point where there are printers designed for home use, and even printer kits are available for the more ambitious.
Additive manufacturing allows the creation of items, some with complex, difficult-to-create interior designs, which would be extremely costly to produce with traditional manufacturing methods. Depending on the method used, surface features of 100 nanometers, as well as complex moving and interlocked parts can easily be produced.
One of the technology’s methods is similar to the common inkjet printer. A 3-dimensional model is generated using a computer, and the printer then deposits microdots of material in layers, gradually building the shape up as the printhead makes repeated passes. A wide range of metals and polymers are applied in this manner. Other methods make use of vats of liquids or gels that are cured by different means, such as lasers or LEDs, in layers that gradually build up the desired structure.
Now, the Guardian reports that the technology is being applied to concrete as a printing material by a research team at Loughborough University. Thus far, they have produced a reinforced concrete bench and a two square meter “S”-curved panel.
According to the Guardian, Richard Buswell, one of the project’s principal investigators, believes that although it is possible, conceptually, to print an entire building, the technology is far more likely to be used to create specially-designed building components.
The research is currently being conducted with a prototype, though Buswell contends that within five years, given sufficient interest and funding, “anything is possible.”
Hyundai Engineering and Construction, Foster and Partners, and Buro Happold have been brought together as industrial partners to evaluate the commercial viability of the project.