Infrastructure protectionShape-memory alloys for earthquake-resistant structures
To improve the performance of structures during earthquakes, researchers have been investigating the use of “smart” materials, such as shape-memory alloys, which can bounce back after experiencing large loads
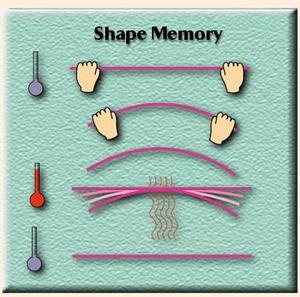
Developing alloys that will remember their original form distortion // Source: talkingelectronics.com
Recent earthquake damage has exposed the vulnerability of existing structures to strong ground movement. At the Georgia Institute of Technology, researchers are analyzing shape-memory alloys for their potential use in constructing seismic-resistant structures.
“Shape-memory alloys exhibit unique characteristics that you would want for earthquake-resistant building and bridge design and retrofit applications: they have the ability to dissipate significant energy without significant degradation or permanent deformation,” said Reginald DesRoches, a professor in the School of Civil and Environmental Engineering at Georgia Tech.
A Georgia Tech release reports that Georgia Tech researchers have developed a model that combines thermodynamics and mechanical equations to assess what happens when shape-memory alloys are subjected to loading from strong motion. The researchers are using the model to analyze how shape-memory alloys in a variety of components — cables, bars, plates and helical springs — respond to different loading conditions. From that information, they can determine the optimal characteristics of the material for earthquake applications.
The model was developed by DesRoches, School of Mechanical Engineering graduate student Reza Mirzaeifar, School of Civil and Environmental Engineering associate professor Arash Yavari, and School of Mechanical Engineering and School of Materials Science and Engineering professor Ken Gall.
A paper describing the thermo-mechanical model was published online 3 February in the International Journal of Non-Linear Mechanics. This research was supported by the Transportation Research Board’s Innovations Deserving Exploratory Analysis (IDEA) program.
The release notes that to improve the performance of structures during earthquakes, researchers around the world have been investigating the use of “smart” materials, such as shape-memory alloys, which can bounce back after experiencing large loads.
The most common shape-memory alloys are made of metal mixtures containing copper-zinc-aluminum-nickel, copper-aluminum-nickel or nickel-titanium. Potential applications of shape-memory alloys in bridge and building structures include their use in bearings, columns and beams, or connecting elements between beams and columns. Before this class of materials can be used, however, the effect of extreme and repetitive loads on these materials must be thoroughly examined.
“For standard civil engineering materials, you can use mechanics to look at force and displacement to measure stress and strain, but for this class of shape-memory alloys that changes properties when it undergoes loading and unloading, you have to consider thermodynamics and mechanics,” explained Yavari.
The Georgia Tech team found that the generation and absorption of heat during loading and unloading caused a temperature gradient in shape-memory alloys, which caused a non-uniform stress distribution in the material even when the strain was uniform.
“Shape-memory alloys previously examined in detail were really thin wires, which can exchange heat with the ambient environment rapidly and no temperature change is seen,” said Mirzaeifar. “When you start to examine alloys in components large enough to be used in civil engineering applications, the internal temperature is no longer uniform and needs to be taken into account.”
To predict the internal temperature distribution of shape-memory alloys under loading-unloading cycles, which could then be used to determine the stress distribution, the researchers developed a model that used the surface thermal boundary conditions, diameter and loading rate of the alloy as inputs.
The team included ambient conditions in the model because shape-memory alloys for seismic applications could operate in a variety of environments — such as water if used in bridge structures or air if used in building structures — which would produce different rates of heat transfer. The researchers used a thermal camera to record the variation in surface temperature of shape-memory alloys experiencing loading and unloading.
Using their model, the researchers were able to accurately predict internal temperature and stress distributions for shape-memory alloys. The model results were verified with experimental tests. In one test, they found that a shape-memory alloy loaded at a very slow rate had time to exchange the heat created with the ambient environment and exhibited uniform stress. If it was loaded very rapidly, it did not have enough time to exchange the heat, leading to a non-uniform stress distribution.
“Our analytical solutions are exact, fast and capable of simulating the complicated coupled thermo-mechanical response of shape-memory alloys considering temperature changes and loading rate dependency,” said Mirzaeifar.
In future work, the researchers plan to examine more complicated shapes and the effects of combination loading — tension, bending and torsion — to optimize shape-memory alloys for earthquake applications.
This project is supported by the Transportation Research Board of the National Academies (Award No. NCHRP-147). The National Academies has rights to the data and the content is solely the responsibility of the principal investigators and does not necessarily represent the official views of the National Academies.
— Read more in Reza Mirzaeifar et al., “Coupled thermo-mechanical analysis of shape memory alloy circular bars in pure torsion,” International Journal of Non-Linear Mechanics (3 February 2012)